Overviews
This wood pellet mill is a vertical pellet mill with the feed hopper installed on top of the wood pellet mill machine. A large space is not required for this machine. Our pellet mill is used as a part of other production lines such as biomass, biofuel, biogas, and the engineering wood manufacturing industry. The machine is also called a wood pellet making machine because it creates pellets from wood.
Optional Configuration
1. Pellet size from die mold of pellet mill
2. Production capacity of the wood pellet mill
3. Power of the pellet mill
Tell us your requirements and we wiil create you custom wood pellet mill.
Application of Wood Pellet Mill
1. creates sawdust pellet, straw pellet, cotton stalk pellet, rice husk pellet, peanut pellet shell pellet, bamboo powder pellet, palm and other plant waste pellet, ash pellet, carbon powder pellet and other chemical raw materials which are difficult to mold and possess poor adhesion
2. Purpose: re-using waste for biofuel plant, biomass power plant, wood processing plant, chemical plant, and wineries.
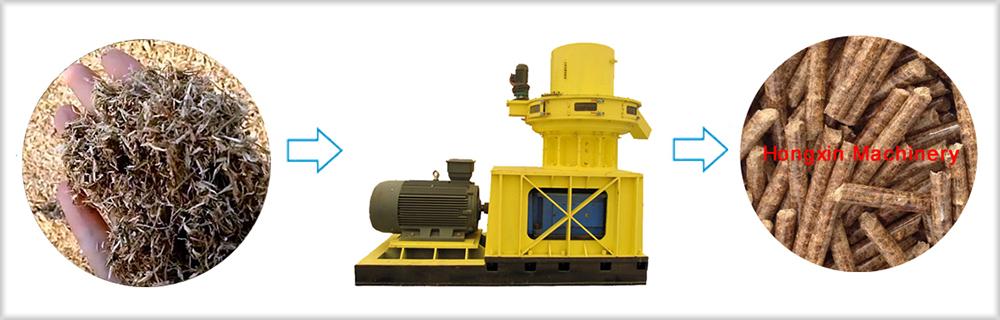
Type | Capacity | Power | Production Size | Weight | Size |
(T/H) | (KW) | (MM) | (T) | (MM) | |
HXZL450 | 0.6-0.8 | 45 | Φ4-12 | 1.3 | 1700x800x1450 |
HXZL470 | 0.8-1 | 55 | Φ4-12 | 2.6 | 1500x1600x1800 |
HXZL560 | 1.2-1.5 | 90 | Φ4-12 | 5.8 | 2600x1300x2310 |
HXZL860 | 2.5-3.5 | 220 | Φ4-12 | 12.6 | 3750x1650X3250 |
More description of the wood pellet mill
1.Power System
The power system is comprised of the Y series motor, coupling, and a high power reduction gear. The reduction gear uses a sound absorption box structure, a large surface area and a large fan. The advanced gear grinding technology improves upon the reliability of the rising temperature, and reduces noise and running, which in turn increases the transmitted power.
2. Granulating Chamber
The granulating chamber consists of the bearing chamber, bearing, main shaft, ring die, compression roller and cutting device. The material with a moisture content of 15 to 18% reaches the granulating chamber and is passed through the feed inlet by the feeding mechanism. The transmission main shaft drives two compression rollers in a rotating manner, and the material is then squeezed into a ring die hole due to said rotation, then squeezed from the compression roller, and shapes in the die hole. After leaving the die hole, the forming particles are cut into the desired length using a cutting device, and flow out of the machine.
3. Lubrication System
The lubrication system is automatic. Lubricating grease is pushed into the main shaft oil hole, lubrication roller bearing and main shaft bearing using an electric oil pump. The system can set injection times and injection interval times automatically based on varied customer requirements.
4.Safety
The wood pellet making machine operates at a fixed location, static working only. The two layer mold’s location may have a switch, which helps to reduce production cost and benefit clients. using cylinder vertical shape to help the cooling radiator to cool off of the chamber temperature. An independent frequency conversion discharge device ensures the particle forming speed. This machine features user friendly and safe operation.
Type | Capacity | Power | Production Size | Weight | Size |
(T/H) | (KW) | (MM) | (T) | (MM) | |
HXZL450 | 0.6-0.8 | 45 | Φ4-12 | 1.3 | 1700x800x1450 |
HXZL470 | 0.8-1 | 55 | Φ4-12 | 2.6 | 1500x1600x1800 |
HXZL560 | 1.2-1.5 | 90 | Φ4-12 | 5.8 | 2600x1300x2310 |
HXZL860 | 2.5-3.5 | 220 | Φ4-12 | 12.6 | 3750x1650X3250 |
Advantages
1. Power System
The power system is comprised of the Y series motor, coupling, and a high power reduction gear. The reduction gear uses a sound absorption box structure, a large surface area and a large fan. The advanced gear grinding technology improves upon the reliability of the rising temperature, and reduces noise and running, which in turn increases the transmitted power.
2. Granulating Chamber
The granulating chamber consists of the bearing chamber, bearing, main shaft, ring die, compression roller and cutting device. The material with a moisture content of 15 to 18% reaches the granulating chamber and is passed through the feed inlet by the feeding mechanism. The transmission main shaft drives two compression rollers in a rotating manner, and the material is then squeezed into a ring die hole due to said rotation, then squeezed from the compression roller, and shapes in the die hole. After leaving the die hole, the forming particles are cut into the desired length using a cutting device, and flow out of the machine.
3. Lubrication System
The lubrication system is automatic. Lubricating grease is pushed into the main shaft oil hole, lubrication roller bearing and main shaft bearing using an electric oil pump. The system can set injection times and injection interval times automatically based on different customer requirements.